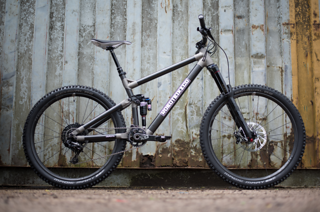
Kurz & knapp
Beim Robot Bike handelt es sich um ein größtenteils maschinell hergestelltes, an jeden einzelnen Kunden individuell angepasstes Fahrrad. Damit stellt es einen krassen Kontrast zur etablierten Massenproduktion dar, die auf großen Stückzahlen und viel Handarbeit in Niedriglohn-Ländern aufbaut. Ermöglicht wird dies durch die Anwendung des 3D-Drucks und einen Geometrie-Automatismus, der basierend auf den Körpermaßen die Fahrradmaße wählt. Weil das alles nicht genug wäre, verwendet Robot Bike außerdem einen von Dave Weagle entwickelten 7-Gelenk-Hinterbau, der auf den Namen DW6 hört und im Grunde einen DW-Link mit einem klassischen Viergelenker kreuzt.
Im Detail
3D Druck
Bereits als wir kürzlich über den von der Airbus-Tocher APWorks gedruckten, integrierten Vorbau berichteten, haben wir damit ein durch metallische, additive Fertigung hergestelltes Fahrradteil gesehen, dass allen realen Belastungen standhält und gleichzeitig in beliebiger Form variiert werden kann, um individuelle Bedürfnisse zu erfüllen. Beim Robot Bike werden die verschiedenen Rahmengeometrien erzeugt, indem die Winkel der durch Laserstrahl-Schmelzen hergestellten Muffen variiert werden. Diese 12 Muffen werden aus Titanpulver, genau genommen pulverisiertem TI6AL4V, aus tausenden etwa 60 µm dünnen Schichten hergestellt, indem ein Laser das Pulver gezielt aufschmilzt. Damit lassen sich auch komplexe Geometrien ohne zusätzliche Werkzeuge herstellen, was die Fertigung eines vieler Einzelstücke nicht wesentlich teurer macht als die Fertigung einer identischen Serie.
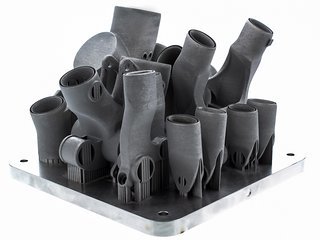
Carbon
Nun könnte man direkt den gesamten Rahmen 3D-Drucken, doch einerseits existiert heute noch keine Maschine mit einem ausreichend großen Bauraum, sodass der Rahmen in Einzelteilen gedruckt und anschließend verschweißt werden müsste (wie bspw. beim APWorks Light Rider), andererseits weisen kohlenstofffaserverstärkte Kunststoffe bessere spezifische Eigenschaften (einfach gesprochen: höhere Steifigkeit und Festigkeit bei gleicher Masse) auf und lassen sich günstiger in einfachen Geometrien herstellen. Damit ergänzen sich die beiden Werkstoffe perfekt: Die feingliedrigen, multi-axial belasteten Rahmenstellen wie beispielsweise das Yoke, der Innenlagerblock, sowie alle Drehpunkte, können im 3D-Druck hergestellt werden. Für die in weniger unterschiedlichen Richtungen belasteten Rahmenbereiche werden Carbon-Rundrohre verwendet, die durch Prepreg-Wickeln maschinell und einfach in hoher Präzision und mit den gewünschten Faserwinkeln hergestellt werden können. Dabei setzen die Briten nicht auf den aus den 2000er Jahren bekannten Carbon-Look, der durch die Verwendung von gewobenen C-Fasern erreicht wird, sondern auf das in den letzten Jahren immer beliebtere uni-direktionale „UD“ Carbon, das noch höhere Steifigkeiten, aber auch eine etwas höhere Delaminationsneigung mit sich bringt.
Muffen
Aus 3D-gedruckten Muffen und CFK-Rohren entsteht ein gemuffter Rahmen. Anders als früher werden Rohre und Muffen jedoch nicht verlötet, sondern verklebt. Kleben ist das sinnvollste Verfahren, wenn es darum geht Carbon-Bauteile zu fügen, da dabei keine Fasern zertrennt werden müssen und die Kraft flächig eingeleitet wird. Um Spannungsspitzen (und damit Schwachstellen) zu vermeiden, werden die Rohre doppelt geschäftet und wie ein Keil in den einige Zentimeter Tiefen, V-förmigen Spalt der Muffe geklebt. So wird eine gleichmäßige Kraftübertragung erreicht, die mit geringen Klebstoffmengen auskommt. Titan ist zusätzlich korrosionsarm, was der Hybrid-Konstruktion zu Gute kommt. Wem Klebstoffe suspekt sind: Flugzeuge und Autos setzen an vielen, auch tragenden Stellen auf hochfeste und automatisierbare Verklebungen.
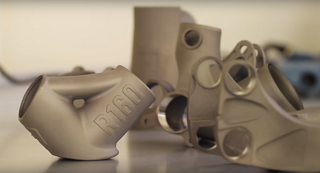
Individuelle Geometrie
Indem nur die Länge der Carbon-Rohre und die Winkel der Titan-Muffen variiert werden, kann virtuell jede Geometrie hergestellt werden. Beide Anpassungen erfordern keine Handarbeit – im Idealfall generiert eine Software aus der vorgegebenen Geometrie nicht nur die benötigten Längen und Winkel, sondern modifiziert auch die CAD-Dateien und das Druck- sowie das Fräsprogramm.
Jeder Kunde soll zu Beginn eines Bestellprozesses drei Körpermaße an Robot Bike übermitteln: Größe, Beinlänge und Arm-Spannweite. Anhand dieser drei Größen schlägt die Firma dann eine Geometrie vor; falls diese von den Kundenwünschen abweicht, wird gemeinsam ein Vorschlag erarbeitet. „Offensichtlich ist der schwierigste Schritt, unsere Geometrie-Automatisierung gut hinzukriegen – aber wir konnten hier auf jahrelange Erfahrung zurückgreifen,“ sagt Ed Haythornthwaite, CEO des Unternehmens, und fügt hinzu: „Wir vermuten, dass viele Fahrer wahrscheinlich nicht wissen, was sie wirklich brauchen und schlagen deshalb immer etwas aus unserer Erfahrung vor. Wenn aber jemand sehr genau weiß, was er will, dann machen wir das. So wollen wir sicher stellten, dass jeder wirklich das Fahrrad/Fahrerlebnis erhält, das er sucht.“
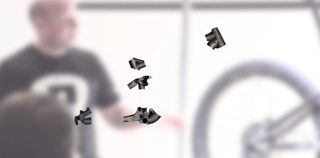
Um einen Geschmack von der Schlagrichtung des Bikes zu geben, gibt Robot Bike auch eine „Standard-Geometrie“ an. Bei dieser liegt der Lenkwinkel bei 65,5°; der Sitzwinkel bei 73,5°. Die Kettenstreben messen 430 mm und das Innenlager liegt 10 mm unter den Radachsen – aber wie gesagt, Individualisierung ist hier die Regel.
Arbeitsbedingungen
Wer sich heute ein hochpreisiges Mountainbike kauft, der kann – mit wenigen Ausnahmen – davon ausgehen, dass dieses in Taiwan oder China in Handarbeit hergestellt wurde. Während es über die Arbeitsbedingungen auch Gutes zu berichten gibt, stellt sich die Frage, eine wie große Gesundheitsgefährdung Prozesse wie Handlaminieren, Schweißen oder Lackieren darstellen und wie gute Lebensbedingungen die gezahlten Löhne erlauben. Einer EOS M290 (einer der populären industriellen 3D-Drucker aus dem Münchner Speckgürtel) oder einer Renishaw AM250 (bei Robot Bike verwendetes, britisches Fabrikat) kann man dagegen nicht zu wenig bezahlen. Und während wir von einer vollautomatisierten Herstellung der gedruckten Bauteile noch ein paar Schritte entfernt sind, ist es nur eine Frage der Zeit, bis auch die Befüllung der Maschinen und die Entfernung von Stützstrukturen automatisiert erfolgen.
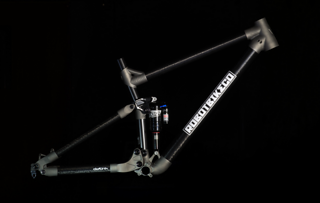
DW6 Hinterbausystem
Als ob die unorthodoxe Rahmenbauweise nicht genügen würde, bekommt dieses Endurobike auch noch einen Hinterbau spendiert, wie man ihn bisher noch nicht kannte. Einfach gesprochen handelt es sich dabei um einen Viergelenker im „Trek Session-Design“, bei dem das Gelenk hinter dem Tretlager durch zwei kurze Umlenkhebel ersetzt wurde: Hinter dem Tretlager sitzt ein Mini-DW-Link, der Rest des Rahmens ist klassischer Viergelenker (Sprich: Wippe am Sitzrohr, Dämpfer steht im Hauptrahmen). Es darf gefragt werden, wozu das nötig ist. Die Antwort von Ed: „Dadurch ist es uns möglich, alle Rahmenparameter (Virtuelle Drehpunktlage, Dämpferkennlinie, Bremsmomenteinflüsse) unabhängig zu optimieren und keine Kompromisse einzugehen. Der Unterschied hinsichtlich der Drehpunktlage mag auf dem Papier klein erscheinen, aber wir glauben, dass Du auf dem Trail begeistert davon sein wirst. Sogar wir waren davon überrascht!“ Um es klar zu sagen: De facto wird sich die Lage des jetzt beweglichen Drehpunktes hinter dem Tretlager nicht gravierend ändern; alles andere würde zu Pedalrückschlag oder sonstigen Antriebseinflüssen führen. Aber: Tatsächlich wird das nur eine Testfahrt klären, ob das zusätzliche Mitführen von mindestens 6 weiteren Kugellagern den Aufwand wert ist. Wie der Name schon sagt, verfügt das Bike über 160 mm Federweg, eine individuelle Anpassung des Federwegs oder der Federkennlinie ist – vorerst – nicht geplant.
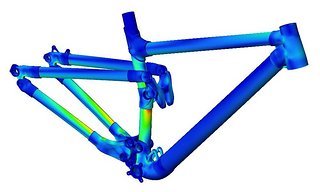
Lebenslange Garantie
Was vielen Bikern nicht klar ist: Aluminium erreicht keine Dauerfestigkeit. Das bedeutet, dass es keine auch noch so geringe Kraft gibt, die das Material über unendlich viele Belastungszyklen hinweg aushalten würde. Anders dagegen Stahl oder eben Titan und, bedingt, auch kohlefaserverstärkte Kunststoffe: Bis zu einem gewissen Belastungslevel sind sie dauerfest. Robot Bike gibt an, den Rahmen so ausgelegt zu haben, dass er keine technisch begrenzte Lebensdauer hat, und gibt konsequenterweise lebenslange Garantie. Abgesichert ist der Rahmen über die in der Luft- und Raumfahrt etablierte Testpyramide, bei der von der kleinsten Materialprobe hin über Fügestellen und Baugruppen hin bis zum kompletten Rahmen mit Prüfstandtests gearbeitet wird; ergänzt durch Tests im echten Leben. Das 6-köpfige Team umfasst mit Ed einen ehemaligen Weltcup-Mechaniker, die Jungs sind in der britischen Szene vernetzt und wissen durchaus, was Fahrrädern heute abverlangt wird.
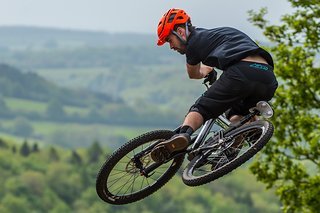
Topologieoptimierung
Wer sich an die Dämpferverlängerung des Alutech ICB2.0 erinnert, dem ist der Begriff der Topologieoptimierung bekannt. Basierend auf mathematischen Beschreibungen wird anhand von Kräften und einem Bauraum die bestmögliche Gestalt für eine Komponente gefunden. Robot Bike hat dieses Verfahren angewendet, zu sehen ist am Rahmen aber relativ wenig davon. Der Grund: Die Klebeverbindungen zu den Rohren geben bereits recht viel vor, nachdem dann zusätzlich noch auf ein einfach zu reinigendes Design geachtet wurde, war man wieder bei recht konventionellen Formen angelangt.
Konstruktion
Es gerät fast zur Randnotiz: Das R160 steht auf inzwischen etablierten 27,5″-Laufrädern und noch stärker etablierten Schnittstellenmaßen: Ein 73 mm BSA-Innenlager und eine 12×142 mm Steckachse sollen maximale Kompatibilität gewährleisten – was angesichts der angestrebten unendlichen Lebensdauer wünschenswert wäre. „Selbstverständlich“ ist der Rahmen mit Teleskopstützen kompatibel. Schönes Detail: Die BSA-Innenlagergewinde stellen die einzigen Gewinde im Rahmen dar. Bei allen Drehpunkten arbeitet man mit Einsätzen, die im Falle eines Falles ausgetauscht werden könnten. Sollte sich in Zukunft doch mal etwas dringliches an den Schnittstellen ändern, will Robot Bikes auch einzelne Module anbieten, etwa neue Sitzstreben zur Anpassung der Ausfallenden oder ähnliches.
Meinung @MTB-News.de
Lebenslange Garantie, individuelle Anpassung und Made in Great Britain – das klingt schon sehr gut! Bis zu einem Test sind wir skeptisch, ob es die zusätzlichen Gelenke am Hinterbau tatsächlich braucht, denn schließlich bedeuten mehr Teile auch mehr Gewicht und ein erhöhtes Risiko, dass doch einmal etwas kaputt geht. Der Preis von etwa 5600 € (Maßrahmen mit Rock Shox Monarch+ Federbein, umgerechnet von 4400 GBP) ist in Anbetracht der Herstellungsweise fast ein Schnäppchen, und dennoch muss man festhalten: Ein maßgeschneiderter, traditionell hergestellter Rahmen Made in Germany ist derzeit nicht teurer, nicht schwerer und erlaubt hinsichtlich der Optik sogar noch mehr Anpassungen. Was jetzt noch fehlt: Passende Komponenten, auf die es ebenfalls lebenslange Garantie gibt – denn hinsichtlich Federung, Schaltung und Rädern ist auch bei diesem gründlich neuartigen Konzept alles beim Alten.
99 Kommentare
» Alle Kommentare im Forumwo isn nu das problem? denke die frage war doch wohl einfach oder nicht?
ich habe in keinster weise die speedhub mies geredet, das sie nicht nur vorteile hat, kann auch nen fanboy zugeben.
hätt ichs kleingeld, denke ich, würd ich se mir in meinen rahmen reinspaxen...
Dieses Fanboy-Gelaber....
on topic:
was mich bzgl des rahmens hier interessieren würde, ob man mit der technik nicht statt carbon auch bambus nehmen könnte...
sorry, kam so rüber...
Wir laden dich ein, jeden Artikel bei uns im Forum zu kommentieren und diskutieren. Schau dir die bisherige Diskussion an oder kommentiere einfach im folgenden Formular: