Zwei Tage vorher
Ein gutgelaunter Trupp europäischer Journalisten, die sich das Fahrradfahren und das Berichten darüber als Passion auserkoren haben, besteigt in Amsterdam den KLM-Flug KL867, der exakt 11 Stunden und 10 Minuten später geschmeidig in Osaka, Japan, aufsetzt. Osaka ist nicht nur die heimliche kulinarische Hauptstadt Japans, sie ist auch die Heimat des Komponentenriesen mit dem charakteristischen Blau – und genau deswegen sind wir hier. Dass Shimano zu einer Media Tour für Journalisten einlädt, ist allein schon ein Novum und das erste Mal seit über zehn Jahren – die Japaner lassen sich, so haben wir es bislang meist erlebt, äußerst ungern in die Karten gucken. Umso mehr ein Grund, unbedingt dabei sein zu wollen. Kaltschmieden, XTR, Massenfertigung – wir sind gespannt, was wir sehen werden. Vorab sei gesagt: Ein gewöhnlicher Hausbesuch wird es nicht.
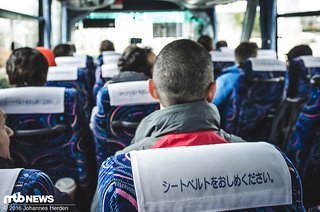
Der erste Tag ist angesichts der frühmorgendlichen Landung für Sightseeing reserviert – akklimatisieren ist angesagt, denn die kommenden Tage sind komplett durchgeplant. Nach der ersten Busfahrt, der noch dutzende folgen sollen, beginnt nun also das Programm, wir besichtigen das Osaka Castle. Ein wiederaufgebautes Kleinod japanischer Architektur, ein fast grüner Ruhepol inmitten dieser großen Industriestadt, die von immergleichen Hochhäusern und nie enden wollenden Stadtautobahnen dominiert wird. Einige touristische Stationen später werden wir im In-Stadtteil Dōtonbori ausgespuckt, wo wir erstmals den ungefilterten Wahnsinn Japans so richtig aufsaugen können.
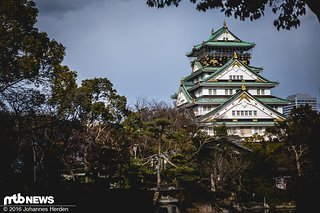
Japanische Innenstädte zeigen das frei heraus, was unter der freundlichen, leisen Persönlichkeit der meisten Japaner sonst verborgen bleibt. Unglaublich laut, unglaublich blinkend, unglaublich schrill ist es hier. Comicfiguren überall, selbst die Wetter-Anzeige am Bahnhof sieht aus wie aus wie aus Super Mario 64. Die kaugummipop-esken Casino- und Spiele-Stores schieben das Niveau nochmal eine Stufe nach oben: alles kracht, alles flirrt, jede Maschine möchte die andere übertönen. Verrückt und zugleich eine Herausforderung für den breiigen Kopf, der nach einer durchgemachten Flugnacht und einem interessanten, aber anstrengenden Tag eigentlich nur noch ins Bett will.
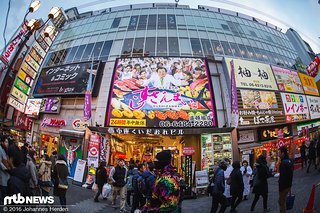
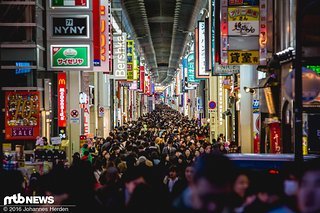
Wir essen Omeletts zu Abend, mitten im quirligen Getümmel in der Stadt, früh am Abend geht es per Bus hinaus aus der glitzernden LSD-Welt. Die Kraft reicht noch für 30 Minuten Fitness und zwei Winterpokalpunkte, dann falle ich ins Bett.
Shimano im Süden: Shimonoseki Factory
Osaka Shinkansen Station. Hier fährt der pünktlichste Zug der Welt im Hochgeschwindigkeit in sämtliche großen Städte Japans, ein einzelner Shinkansen-Zug hatte im Jahresschnitt 2005 ganze 6 unplanmäßige Sekunden. Unser Shinkansen hat heute 50 Minuten Verspätung.
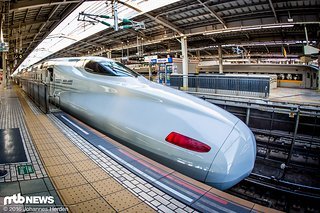
Für uns aus Deutschland fast normal, für die Japaner nicht. Im südlicheren Landesteil hat es ein wenig geschneit, ein paar Zentimeter. Diese dünne weiße Schicht wird in München oder selbst in Köln mit einem Schulterzucken hingenommen, im Land der aufgehenden Sonne nimmt solch ein Wetter-Ungetüm armageddonsche Ausmaße an: die Züge zu spät, die Autobahn gesperrt, die Autofahrer ziehen panisch Schneeketten über die Reifen. Irgendwann kommt der Zug eingefahren und wir haben, und das ist ernst gemeint, das entspannteste und komfortabelste Zugerlebnis aller Zeiten. Nach weiteren 90 Minuten Busfahrt (die Autobahn ist ja gesperrt) erreichen wir Shimonoseki. Hier befindet sich neben einem piekfeinen, neuen Hauptgebäude die zweite von Shimano je erbaute Fabrik überhaupt, und nach einem schnellen Mittagessen (12 Minuten, wir sind schneebedingt stark verspätet) kommt schon die erste, freundliche Leiterin der Führung und erklärt das folgende Prozedere, das an uns fast vorbeigeht, wäre da nicht ein bereits erwähntes, aber leider immer noch durchgestrichenes Kamerasymbol. 23 Fotografen fluchen. Innerlich.
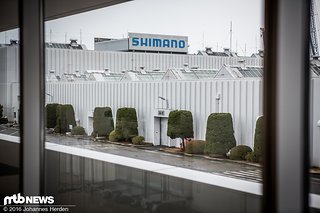
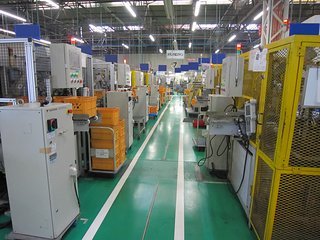
Dieser Hausbesuch ist anders als alle bisher. Hatten wir bislang meist relativ freien Zugang in anderen Firmen, sobald die wichtigen Teile versteckt oder abgedeckt worden waren, so besteht der erste Tag der Shimano Media Tour aus präzisen 30 Minuten Führung. In Shimonoseki wird gestanzt, gedreht und verschickt: Hier werden unter anderem die Rennrad-Gruppen Tiagra und 105 gefertigt, auf Mountainbike-Seite entstehen Saint und XT-Kurbeln, außerdem werden die Schaltungsnaben Nexus und Alfine hier gefertigt.
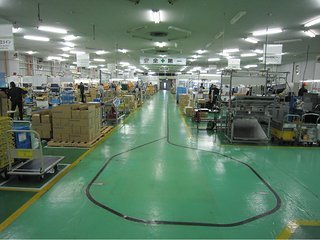
Das Besondere daran: alles, aber wirklich alles, geschieht in-House. Das Rohmaterial wird fertiggemacht; je nach Produkt gestanzt oder geschmiedet, wärmebehandelt, befräst und finalisiert, am Ende in große Boxen gepackt und auf die Reise geschickt. Die Ausstattung der Firma ist schon beeindruckend: neben einigen Dutzend Mitarbeitern übernehmen grosse Roboterarme hier einem Großteil der Aufgaben und greifen sich präzise Kurbel für Kurbel, die durch alle Arbeitsschritte geleitet werden. Unser japanischer Gruppenführer drückt allerdings aufs Gas. Nach exakt 30 Minuten spuckt uns die riesige Halle 300 Meter weiter wieder aus. Eile ist angemahnt, denn der Zug zurück nach Osaka muss rechtzeitig erreicht werden. Schon sitzen wir wieder im Bus, eine knappe Stunde waren wir vor Ort.
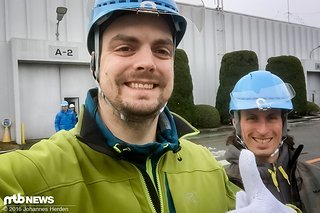
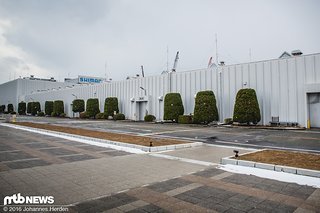
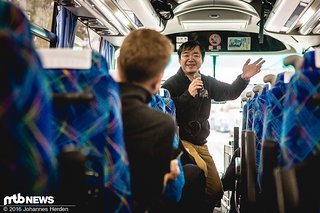
So ganz wissen wir noch nicht, was gerade passiert ist. 23 leicht ratlose Mienen sitzen im Schnellzug zurück nach Osaka und haben heute realisiert, was der japanese way of presentation ist, der sich mit einem Shinkansen Zug in Bestform vergleichen lässt: Präzision, Effizienz, on Time, kein Schnickschnack. Nach 11 Stunden Fahrt am heutigen Tag, deren Ziel eine halbstündige Präsentation im japanischen Niemandsland war, fallen wir erschöpft in die Betten, mit Blick auf das in der Nacht lichterflirrende Osaka.
Im Herzen Japans: Shimano in Sakai und Osaka
Shimano Hauptquartier & High Tech Production plant
Die Zeit im Reisebus wird heute kürzer ausfallen, denn das Shimano Hauptquartier in Sakai steht heute an. Neben dem Hauptquartier befindet sich die High Tech Production Plant, wir sind gespannt, was wir heute sehen werden.
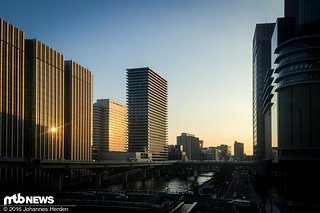
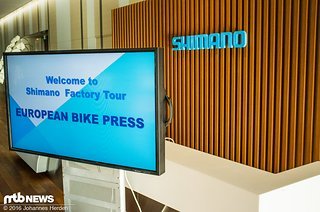
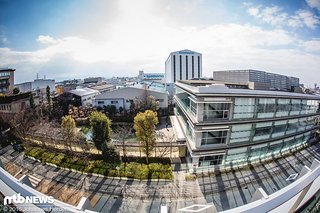
Das Wetter zeigt sich heute von seiner besten Seite. Keine Minusgrade, kein Schnee, Sonne pur. Als unser Bus vor dem Hauptquartier einfährt, herrscht auf einmal hektische Betriebsamkeit. Ein Fotograf positioniert sich, Angestellte machen sich bereit und schwupps ist die europäische Reisegruppe inklusive Shimano-Belegschaft vor dem Eingang auf einer japanischen Speicherkarte verewigt. Ein Mannschaftsfoto, dass nicht zum letzten Mal auf dieser Reise gemacht werden wird. Das brandneue Hauptquartier ist imposant: viel Holz, viele japanische Leichtigkeit, Perfektion in allem. Wie schon gestern werden wir in den Konferenzsaal gebeten und auch der arme durchgestrichene Fotoapparat fehlt nicht. Heute dürfen nicht einmal mehr Blöcke und Stifte mitgenommen werden, Sicherheitsbestimmungen.
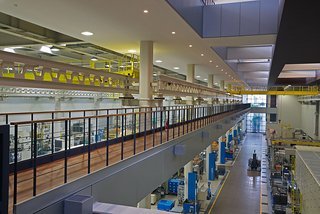
In der High Tech Production Plant im Hauptquartier im Herzen Sakais werden die Edelkurbeln Shimanos hergestellt, hier wird aus einem Stück Aluminium die XTR-Kurbel. Generell ist die Zentrale auch produktionstechnisch die Basis eines jeden neuen Produktes: Die Produktion eines jeden Produktes geschieht zuerst immer in der Stadt des Firmensitzes. Maschinen werden gebaut, eingestellt, der Produktionsablauf strukturiert. Sobald die Produktion erprobt wurde und alles einwandfrei funktioniert, wird diese in die Shimano-Fabriken auf der ganzen Welt exportiert – keine Ausnahmen. Japanische Gründlichkeit.
Wie schon seit gestern bekannt, hat es die freundliche, aber bestimmte Leiterin der Führung recht eilig, aber eindrucksvoll ist es: Diese Firma ist die wohl modernste, was ich je gesehen habe. Nichts liegt herum, alles ist blitzeblank sauber, wir haben von unseren Stegen, von denen man aus rund 8 Metern nach unten in die Hallen guckt, einen guten Ausblick. Gabelstapler und andere Fahrzeuge sind hier ferngesteuert und fahren von Halle zu Halle, drehen wieder um und liefern ab. Dabei spielen die eigentlich geräuschlosen Fahrzeuge Musik, um eventuell auf der Spur laufende Arbeiter vorzuwarnen. Höchste Effizienz, Hightech pur. Kameras wären hier zudem fast nutzlos gewesen, denn die riesigen Maschinen geben kaum etwas von ihrem Inhalt preis. Das weiß auch Shimano und hat daher nach jeder Station eine schmucke Galerie des jeweils produziertem Produktes aufgebaut, in Verbindung mit einem erklärenden Video auf einem Flatscreen-Monitor.
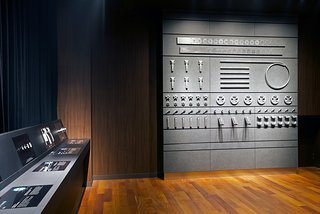
Wer einmal die Produktionsschritte einer XTR-Kurbel gesehen hat, möchte sich vor den Ingenieuren verneigen und beginnt zu verstehen, warum Shimano weiterhin auf Aluminium-Kurbeln setzt statt auf Kohlefaser. Denn diese wird kaltgeschmiedet (wie Schmieden Schritt für Schritt funktioniert, erfährt der interessierte Leser am Ende dieses Artikels): Ein simpler, zylindrisch geformter Aluminium-Rohling wird vom einem geschäftigen Roboterarm in die Mold gelegt und mit japanischer Sanftheit von einer Presse mit unglaublichem Druck in eine perfekte Form gedrückt. Nichts steht über, kein Material wird verschwendet. So, wie diese Kurbel in Form gequetscht wird, bleibt sie auch, präzise auf den Hundertstel-Millimeter. Dieser Prozess nennt sich Kaltschmieden und hat gegenüber einer CNC-gefrästen Kurbel einen entscheidenden Vorteil: Während beim Fräsen die innere Struktur des Metalls gleich bleibt und sich nur die äußere Struktur ändert, passt sich beim Schmieden der innere Gitteraufbau des jeweiligen Metalls an die Kontur der Mold an, was später einen deutlich besseren Kraftfluss zulässt. Des Weiteren wird das Metall kaltverfestigt, ist also nach dem Schmieden deutlich fester als zuvor. Da eine gewisse plastische Verformung bereits erfolgt ist, sind höhere Kräfte notwendig um es weiter plastisch zu verformen.
Pro Kurbel kommen zwei dieser Rohlinge zum Einsatz: aus dem größeren werden Spider und größerer Teil der Kurbel, aus dem kleineren das Oberteil geschmiedet. Im Anschluss werden die beiden Teile zusammengesetzt: dies geschieht allerdings nicht durch einen Schweiß-, sondern eine Kombination aus Schmieden und Kleben: Ein Spezialkleber wird aufgetragen, die 100% passgenauen Stücke miteinander verbunden. Der Kleber wird per UV-Strahlung aktiviert und verbindet die Teile bombenfest, abschließend wird die Kurbel für Haltbarkeit und Steifigkeit nochmals gehärtet.
Das schicke Äußere einer jeden High End-Kurbel wird zum Schluss nicht einfach lackiert oder besprüht – um die charakteristischen titanfarbenen und schwarzen Akzente zu setzen, wird die Kurbel, nach einer vorherigen Maskierung von Logo oder Schriftzug, in verschiedene Flüssigkeiten getaucht. In einer mehrteiligen Prozedur reagieren Kohlenstoff-Partikel mit dem Aluminium der Kurbel und haften an. Eine haltbare und sehr präzise Variante der Farbgebung, denn den Grautönen sind keine Grenzen gesetzt: Für eine dunklere Farbe wird der Prozess einfach wiederholt. 50 Shades Of Grey, quasi.
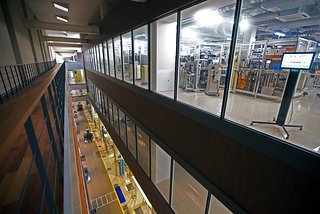
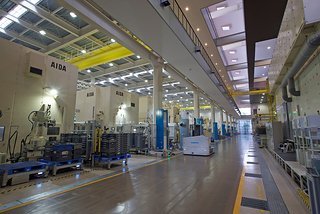
Ein Geheimnis bleibt weiterhin die Kurbel-Produktion der hochwertigen zweiten Schaltgruppen, XT und Ultegra. Diese werden nicht geklebt, sondern hohlgeschmiedet: dabei sollen die Kurbeln auf einem Dorn geschmiedet werden, welcher den Hohlraum erzeugt – dieser soll im Anschluss durch einen weiteren Schmiedevorgang verschlossen werden, Schweissnähte findet man an diesen Kurbeln keine, weitere Infos seitens Shimano ebenso wenig – mit einem verschmitzten Lächeln werden Nachfragen zum Thema mit einem „Exactly how we do that is part of the magic of our Hollowtech technology“ beantwortet.
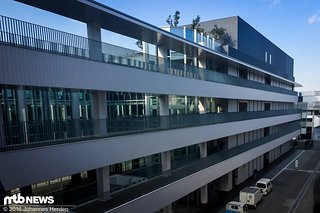
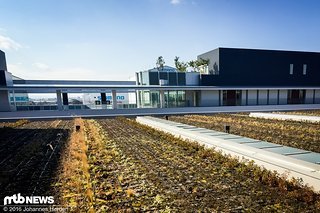
Die Führung neigt sich dem Ende und es geht nahtlos durch diverse Galerien und Außengänge Richtung Mittagessen. Die Flachdächer der Shimano-Gebäude sind begrünt, viel Licht scheint durch die Etagen. Reduziertes, elegantes, funktionelles Design – das passt durchaus zu den Firmenprodukten. Unsere Tour endet nach einer Diskussionsrunde im Empfangsgebäude, hier wird nochmals gefachsimpelt: Die Rennradler mit Tsutomu Muraoka and Takao Harada, wir Mountainbiker mit Kichinosuke Kubo and Taketoshi Sato – den japanischen Produktmanagern im Bereich Mountainbike. Auch hier setzt sich die Firmensprache weiter fort: Ein riesiger, blitzsauberer Raum mit eleganten Schaukästen, welche die wichtigsten Produkte Shimanos beherbergen. Neben den MTB- und Rennrad-Produkten gehören auch die Hightech-Angeln dazu, die Shimano ebenfalls produziert.
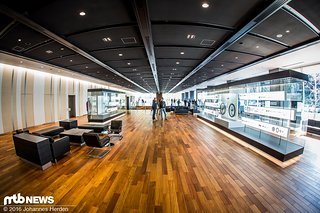
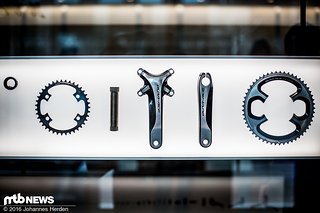
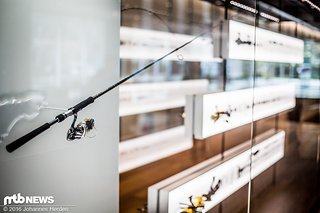
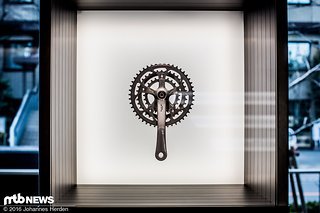
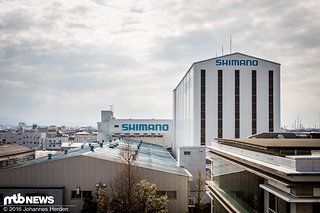
Der Tag ist noch lang, wir müssen los. Der Bus rollt vom Gelände des vom Empfangsbereich aus fast ein wenig unscheinbar wirkenden Hauptquartiers von Shimano. Einem kleinen, hellen Lichtblick im Herzen der grauen Industriestadt Osaka.
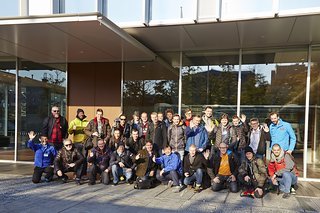
Sakai Bike Museum
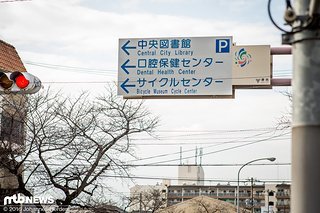
Still und leise sind die Straßen, bis auf wenige Autos ist in diesem Bereich Sakais kaum etwas los. Und auch deswegen würde man nicht glauben, dass in diesem unscheinbaren Bereich Sakais ein Gebäude mit unglaublichen Fahrradschätzen liegt – unterstützt von Shimano. Das Sakai Bicycle Museum ist ein grauer Klotz, dem man nicht ansieht, dass innen vermutlich mehr europäische Bike-Originale lagern als in Europa.
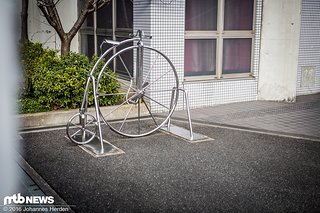
Zu wenig Zeit für zu viele Bikes! Erste Laufräder aus Holz und primitiven Lenkstangen bis hin zu Dreirädern, verrückten Antrieben bis hin zu den ersten Rennrädern in Europa, die mit japanischen Shimano-Schaltgruppen ausgerüstet wurden. Ein wertvolles Original durfte nicht fehlen: Eins von zehn je gebauten 1978er Breezer Bikes, mit denen schon damals bei den Repack-Rennen in Marin County die Hügel hinuntergebrettert wurde.
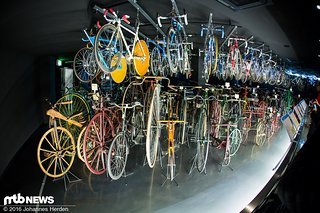
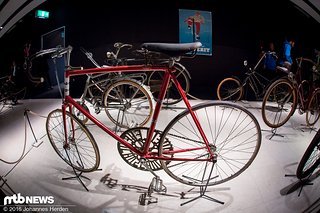
OVE Store
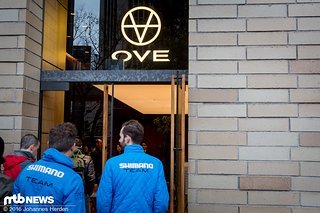
Ein smarter Ruhepol mitten im Herzen Osakas ist der OVE Store. Ebenso wie das Bicycle Museum augenscheinlich keine Produktionsfirma, aber dennoch ein wichtiges Projekt von Shimano: Eins der Ziele der Japaner ist nämlich, das Fahrradfahren noch mehr in das tägliche Leben mit einzubeziehen. Der OVE Concept Store ist hierzu 2006 eröffnet worden und soll als entspannender Ort inmitten der hektischen Stadt dienen, in dem man in interessanten Bikebüchern schmökern, sich in den tiefen Sesseln fläzen oder schicke (aber teure!) Klamotten zum Biken und Drumherum erwerben kann. Einmal wöchentlich gibt es auch die Möglichkeit, dem direkt vom OVE Store startenden City Ride teilzunehmen.
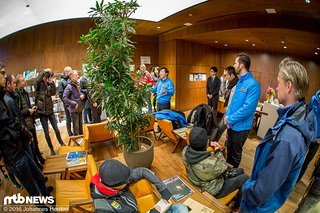
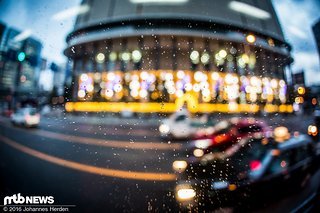
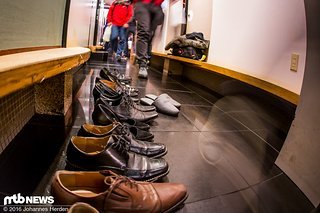
Es dämmert, ein langer Tag geht zu Ende. Wir haben viel gesehen, viel gehört und sind noch mehr Bus gefahren – und befinden uns trotzdem immer noch mittendrin in der Reise. Nach einem Abendessen in der Stadt geht es auch schon wieder ins Hotel, es gilt, die Tasche rechtzeitig zu packen. Der zweite Teil des Trips steht an, hin kommen wir frühmorgens mit dem Flugzeug und wir sind noch ungewiss, was uns erwartet. Was sicher sein wird:
1) Wir bleiben in Asien
2) Es wird 30 Grad wärmer sein
Lasst euch überraschen – übermorgen geht es weiter!
Exkurs: Schmiedevorgang
Vor Ort bekamen wir nicht alle Einzelheiten so präzise erklärt, wie wir es vielleicht gerne gehabt hätten – unser Redaktions-Ingenieur Thomas Fritsch umreißt für alle Interessierten einmal grob einen generellen Schmiedevorgang und speziell die Besonderheiten bei Shimano, soweit es bekannt ist.
Material auswählen
- Ausgangsrohling wird aus Blech gestanzt oder gelasert
- Rohling wird in Negativ Form eingelegt und durch große Kräfte umgeformt
- Je nach Komplexität sind mehrere Umformvorgänge notwendig (hierfür gibt es jeweils eine eigene Form)
- Nach dem letzten Vorgang wird in den meisten Fällen überstehendes Material (Grate) entfernt. Shimano fertigt seine Bauteile im so genannten Präzisionsschmieden (der Ausgangsrohling ist so präzise ausgeschnitten, dass kein Grat entsteht und somit auch kein Abfall)
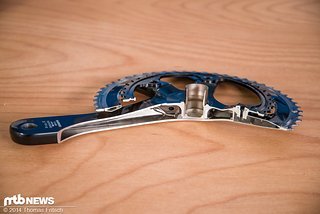
Vorteile von Schmieden im Vergleich zum Fräsen
- höhere Festigkeit durch materialflussgerechte Gitterstruktur
- höhere Steifigkeit durch Kaltverfestigung
- beim Präzisionsschmieden entsteht kein Abfall (Späne) dadurch deutlich umwelt- und ressourcenschonender
- Nachbearbeitung sind beim Präzisionsschmieden nicht notwendig. Die Maßhaltigkeit ist genauer
- Die Oberflächenbeschaffenheit ist, direkt aus der Maschine, besser. Je glatter die Oberfläche, desto höher die Dauerfestigkeit
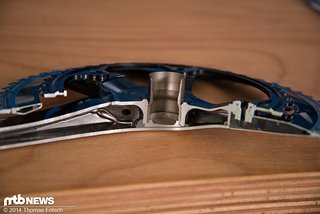
Warum schmiedet dann nicht jeder?
- Eine Presse kann gut und gerne bis zu mehreren Millionen Euro kosten
- Je Umformvorgang ist eine eigene Form notwendig, welche je nach Größe ca. 100 000 € kostet
- Mit einer Fräse lassen sich Teile direkt herstellen, eine Presse benötigt Vor- und je nach Genauigkeit eine Nachbearbeitung
- der Prozessablauf ist sehr kompliziert und benötigt eine monate-, wenn nicht jahrelange Einstellung bis die richtige Materialstärke, Schmierstoffmenge und Position, Hubkraft und Geschwindigkeit herausgefunden wurde. Die Bleche fangen an zu reißen, wenn einer der Parameter falsch eingestellt ist. Beim Fräsen muss nur der materialabhängige Vorschub eingehalten werden – dies ist im Verhältnis relativ schnell ausgerechnet.
90 Kommentare
» Alle Kommentare im Forumsupergute Glaskugel
http://www.mtb-news.de/news/2016/02/29/shimano-2017-neue-kettenblaetter-gangabstufungen/
11-46 in schwer
bin schon gespannt auf die SRAM 1x12 mit 10-46 Kassette
Die Ankündigung wirkt auf jeden Fall reichlich früh. Von den Kettenblättern gibts grad mal eine Skizze, von der Kassette überhaupt kein Bildmaterial und nur ein "Zielgewicht". Das legt nahe, dass von den eigentlichen Produkten allenfalls Prototypen existieren. Vll. ist Shimano an den Punkt angekommen, an dem der quasi-Verlust eines Marktsegments so richtig schmerzt. Oder sie wollen dem drohenden Hype um die SRAM Eagle (mit 10-50) ein bißchen Wind aus den Segeln nehmen.
Zumindest bei den Kettenblättern gibt es ja anscheinend schon das ein oder andere Patent um Gewicht einzusparen:
http://www.bikerumor.com/2016/02/01...h-to-make-lighter-better-shifting-chainrings/
Klar klingt plausibel...wie viele Leute haben auf Shimano 1x11 gewartet um dann feststellen zu müssen dass es gegenüber Sram 1 x11 eigentlich eher eine halbgare Sache ist. Weniger Bandbreite, ne 2x11 Gruppe die keiner wirklich braucht und sackschwere Kassetten - gut bleibt der günstigere Preis. Sie wollen die Leute vermutlich weiter bei der Stange halten bevor 1x12 kommt. Eigentlich habe sie sich
mit der aktuellen Ankündigung eingestanden dass sie sram da momentan hinterherhinken.
#64 Wie genau die unterschiedlichen Bauteile gefügt werden lässt sich nur erahnen - Vorschläge? - Eventuell Kurbelarme hohlgeschmiedet und Achse verklebt ?
---
Die Achse wird von aussen durchgeschoben, wie man sieht. Jetzt stellt sich die Frage, wie das überhaupt möglich ist, bei der ganzen Schmiederei drumherum?
Wir laden dich ein, jeden Artikel bei uns im Forum zu kommentieren und diskutieren. Schau dir die bisherige Diskussion an oder kommentiere einfach im folgenden Formular: