Nach über drei Jahren Entwicklung, Tests und Anpassungen ist es jetzt soweit: Mit dem heutigen Launch der neuen Website startet bei Atherton Bikes der Verkauf. Nachdem bereits im Februar letzten Jahres eine auf 100 Stück limitierte Auflage an treue Fans verkauft wurde, können sich Kunden in der ganzen Welt ab sofort ihr persönliches Bike aus der Feder von Rachel, Gee und Dan bestellen.
Alle Infos zur Bike-Marke und den Hintergründen erfahrt ihr in unserer umfangreichen Vorstellung von Atherton Bikes oder dem Interview mit Ingenieur Ed Haythornthwaite.
Jedes Rad wird auf Bestellung gefertigt und ist für die Ewigkeit gebaut, sodass es keinen Abfall gibt. Wir alle lieben es, wenn wir unsere Bikes auf den Trails sehen. Wir befinden uns definitiv noch in der Start-up-Phase, aber ich hoffe, dass diese nächste Phase der Unternehmensentwicklung noch viel mehr Menschen die Chance gibt, unsere Bikes auszuprobieren.
Weltmeisterin Rachel Atherton
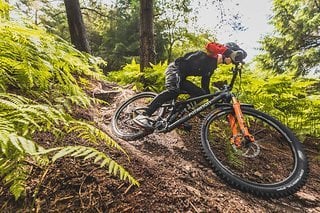
Zur Markteinführung werden vorerst zwei Modelle angeboten: Das allseits bekannte Downhill- Racebike mit 200 mm Federweg und eine neu verfeinerte Version des 29″-Enduro-Bikes mit 150 mm Hub. Weitere Produktneuheiten sollen noch dieses Frühjahr folgen.
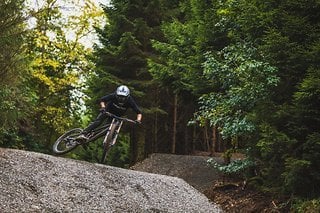
Alle Atherton Bikes werden in Wales mithilfe der additiven Fertigung hergestellt. Durch die Kombination von 3-D-gedruckten Titan-Muffen mit Carbon-Rohren lassen sich spielend einfach unterschiedliche Geometrien realisieren. Diese Technologie ist in der Formel 1 und in der Luft- und Raumfahrtindustrie weit verbreitet, im Mountainbike-Bereich ist sie jedoch noch relativ unbekannt.
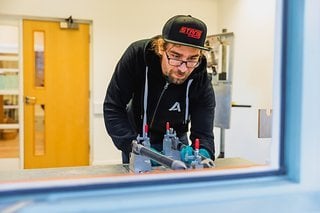
Im Gegensatz zu den meisten High-End-Marken verlassen wir uns nicht auf Carbon-Moulds oder die Produktion in Fernost. Jedes unserer Fahrräder wird individuell im CAD zugeschnitten, um Titan-Muffen zu produzieren, die mit einem für die Luft- und Raumfahrtindustrie geeigneten Klebstoff an die Kohlefaserrohre geklebt werden. Unsere Räder sind nicht nur sehr stabil, sondern wir können auch schnell reagieren und haben ein enormes Potenzial für Variationen in Größe und Geometrie sowie für die Einbindung neuer Erkenntnisse in einen kontinuierlichen Verbesserungsprozess.
Dan Brown, CEO Atherton Bikes
Auf der neuen Website findet sich ein Passform-Rechner, der Kunden eine der vielen Standardgrößen vorschlägt. Derer gibt insgesamt satte 22 beim Enduro-Bike sowie 12 beim Downhiller. Alternativ besteht zudem noch die Möglichkeit, sich eine ganz persönliche Custom-Geometrie anfertigen zu lassen.
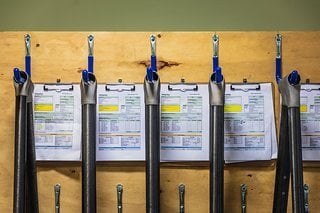
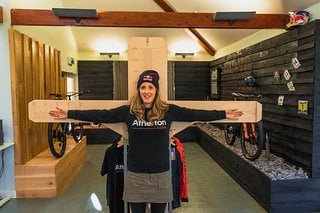
Die additive Fertigungstechnologie, die diese Vielseitigkeit ermöglicht, beseitigt auch die Einschränkungen eines dreijährigen Produktzyklus. Das bedeutet, dass die Erkenntnisse von der Rennstrecke oder aus den kontinuierlichen Tests im Dyfi Bike Park sofort in die Produktionsräder einfließen können. Zeitgleich mit dem Start der neuen Website hat das Produktteam eine Reihe von Verbesserungen am Enduro-Bike vorgenommen: Das neue Atherton Bike 150 verfügt über Kabelführungen, einen Unterrohrschutz, einen steileren Sitzwinkel sowie eine tiefer versenkbare Sattelstütze.
Preislich geht es bei £ 3.999 für den Rahmen oder £ 6.700 für die Komplettbikes los.
Es war schon immer unser Traum, ein Fahrradunternehmen mit dem Namen Atherton zu gründen. Wir begannen, Formel-1-Technologie und Luft- und Raumfahrttechnik zu nutzen, um in Wales Mountainbikes herzustellen, was für uns und unseren Wunsch, Dinge anders zu machen, aufregend war.
Dan Atherton
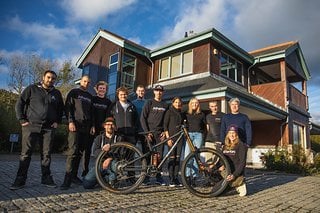
Weitere Informationen unter www.athertonbikes.com
Wie gefallen euch die Bikes?
136 Kommentare
» Alle Kommentare im ForumDanke, ich hatte das Video zwar schon mal angeschaut, aber jetzt ist mir das noch mal etwas klarer. In ein paar der Muffen sind also noch mal Muffen eingearbeitet die quasi innen in die Carbonrohren gesteckt werden. Zudem scheinen sie generell relativ viel Wert auf eine gute Verbindung der Muffen mit den Rohren zu legen, es sieht so aus als ob da auch noch Öffnungen sind die entweder noch mal mit Kleber gefüllt werden und / oder in die evtl. sogar noch Nieten oder Schrauben eingesetzt werden.
Wenn ich mich nicht täusche sind die "doppelten" Muffen aber nicht an allen Stellen. Es wäre natürlich interessant ob dadurch generell wirklich eine höhere Stabilität erreicht wird oder das nicht auch anders / einfacher gelöst werden könnte (und sie so vielleicht einfach nur auch langfristig auf Nummer sicher gehen wollten, bzw. die Möglichkeiten des 3D Druckes einfach voll ausschöpfen). Ich habe ein paar klassische Carbon-Muffen-Rahmen in meiner Sammlung und werde mir die mal genauer anschauen, ich glaube so ganz primitiv waren die auch nicht gearbeitet. Direkt gesehen habe ich auch noch keinen bei dem sich die Klebeverbindung gelöst hat. Eine Statistik dazu wäre interessant, bei den Titanal Rahmen sind es meiner Einschätzung nach ja deutlich mehr als die Hälfte gewesen die gerissen sind, ich denke die Carbon-Muffen-Rahmen haben weit weniger schlecht abgeschnitten. Wenn ich mal einen der klassischen Rahmen in die Hände bekomme der unwiderruflich kaputt ist werde ich ihn auch mal auseinandernehmen und mir die Verbindungen dann noch genauer anschauen können (auf einen kaputten Atherton muss ich bestimmt noch ein paar Jahre warten).
Im Sommer einen Thread aus dem Winter ausgraben...ja es tut mir leid.
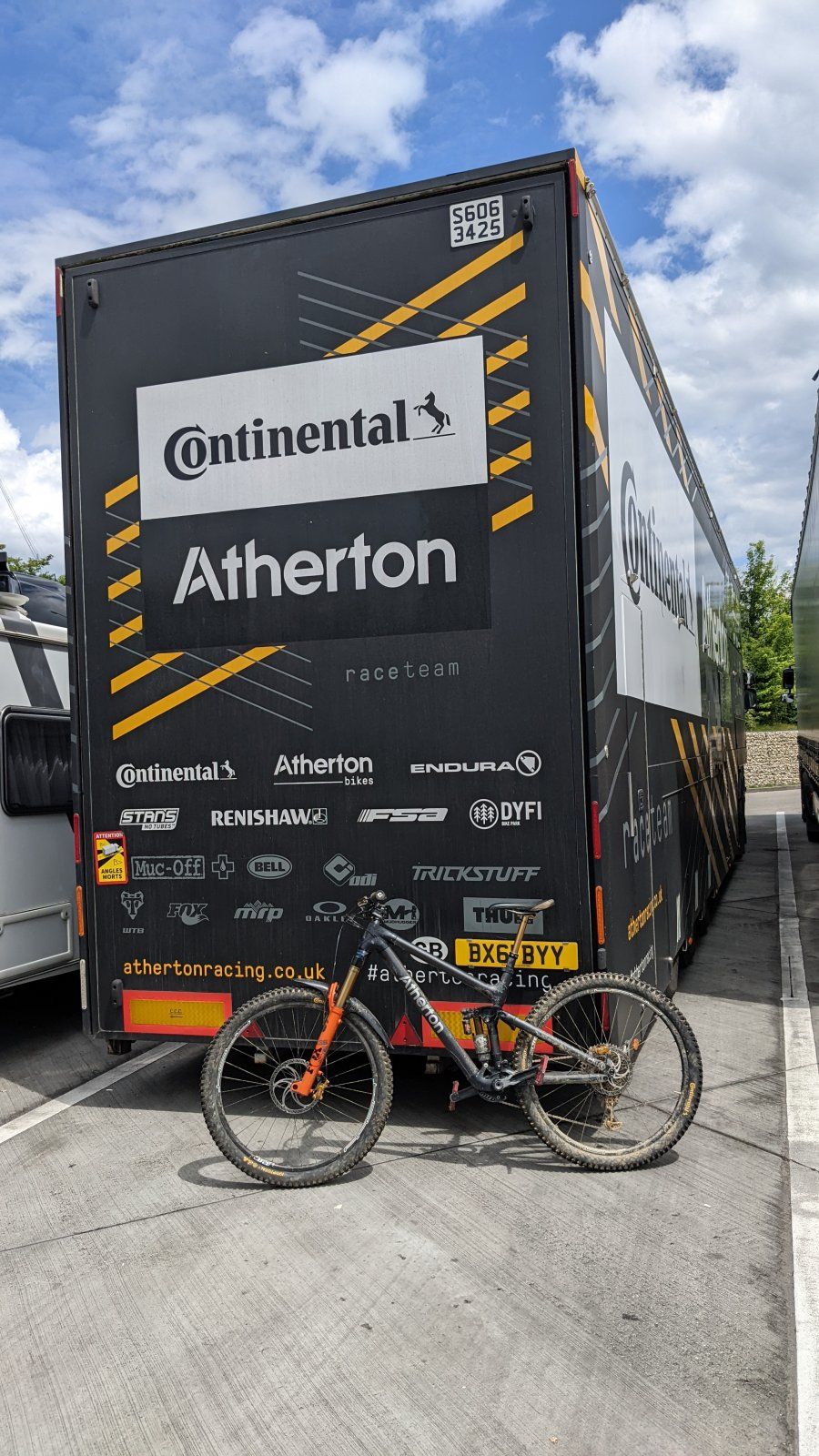
Gestern am richtigen Rastplatz gehalten und zufällig den Team-LKW auf dem Weg nach Leogang gesehen.
Geiler Hobel! Also LKW wie auch Bike.
Und so sieht der Partybus von innen aus:
Warum steht da zufällig ein Bike am Partybus auf dem Rastplatz; sind die vom Toilettendach gesprungen?
Wir laden dich ein, jeden Artikel bei uns im Forum zu kommentieren und diskutieren. Schau dir die bisherige Diskussion an oder kommentiere einfach im folgenden Formular: